Kraken 5at
Генпрокуратура Франкфурта-на-Майне, Центральное управление по борьбе с интернет-преступностью и федеральная уголовная полиция сообщили об аресте серверов крупнейшей в мире kraat даркнет-площадки «ОМГ» (omg Market). Речь идёт о крупнейшей площадке для торговли наркотиками и крадеными данными.Германия вела расследование против omg Market с августа 2021 года при содействии США. Если верить правоохранителям, им удалось изъять биткойны на kracc сумму, эквивалентную примерно 23 миллионам евро. На данный момент это немногим менее 500 биткойнов.Нелегальная торговая площадка omg Market представляла собой русскоязычную платформу даркнета, доступ к которой через сеть Tor был как минимум с 2015 года. Их внимание было сосредоточено на торговле наркотиками, кроме того, через платформу предлагались украденные личные данные, поддельные документы и цифровые услуги.Сейчас силовики пытаются установить операторов и администраторов «Гидры». Их хотят привлечь за торговлю наркотиками, эксплуатацию криминальных площадок и отмывание денег.На торговой площадке было зарегистрировано около 17 миллионов клиентов и более 19 000 продавцов. Эксперты утверждают, что среди нелегальных ресурсов «ОМГ» имела самый большой оборот в мире — только за 2020 год он составил не менее 1,23 миллиарда евро.
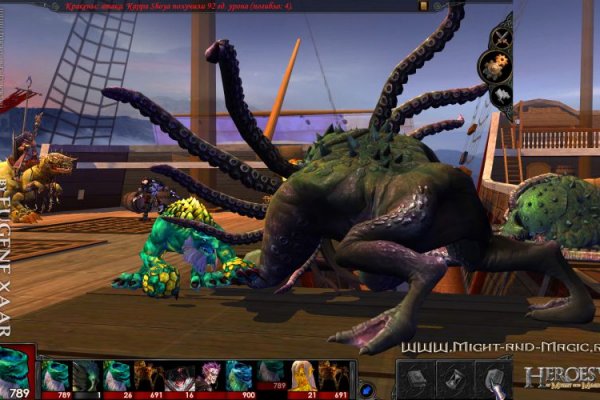
Kraken 5at - Kra28.cc
Onion - secMail Почта с регистрацией через Tor Программное обеспечение Программное обеспечение e4unrusy7se5evw5.onion - eXeLaB, портал по исследованию программ. Основные усилия направлены на пресечение каналов поставок наркотиков и ликвидацию организованных групп и преступных сообществ, занимающихся их сбытом». Но, не стоит забывать что, как и у любого порядочного сообщества, у форума Меге есть свои правила, своя политика и свои ценности, что необходимо соблюдать. 2 Как зайти с Андроид Со дня на день разработчики должны представить пользователям приложение Mega для Android. Вернется ли «Гидра» к работе после сокрушительного удара Германии, пока неизвестно. Кто чем вместо теперь пользуется? Playboyb2af45y45.onion - ничего общего с журнало м playboy journa. Лишь после полной оплаты штрафа продавец сможет вернуться на площадку. Тем не менее, для iOS существует великолепное приложение Tor. Onion - OutLaw зарубежная торговая площадка, есть multisig, миксер для btc, pgp-login и тд, давненько видел её, значит уже достаточно старенькая площадка. Обратите внимание, года будет выпущен новый клиент Tor. Но сходство элементов дизайна присутствует всегда. Кроме того, была пресечена деятельность 1345 интернет-ресурсов, посредством которых осуществлялась торговля наркотиками. Хотя слова «скорость» и «бросается» здесь явно неуместны. Встроенный в Opera сервис VPN (нажмите). Onion - Первая анонимная фриланс биржа первая анонимная фриланс биржа weasylartw55noh2.onion - Weasyl Галерея фурри-артов Еще сайты Тор ТУТ! Opera, Mozilla и некоторых других. Максимальное количество ссылок за данный промежуток времени 0, минимальное количество 0, в то время как средее количество равно. За активность на форуме начисляют кредиты, которые можно поменять на биткоины. Сайт разрабатывался программистами более года и работает с 2015 года по сегодняшний день, без единой удачной попытки взлома, кражи личной информации либо бюджета пользователей. Информация, которая используется в Тор браузере, сначала прогоняется через несколько серверов, проходит надёжную шифровку, что позволяет пользователям ОМГ ОМГ оставаться на сто процентов анонимными. Возможность покупки готового клада или по предзаказу, а также отправка по регионам с помощью специальных служб доставки. Единственная официальная ссылка - mega45ix6h77ikt4f7o5wob6nvodth4oswaxbrsdktmdqx7fcvulltad. Пароль. Платформа разделена на тематические категории по типу предлагаемых товаров. Этот и другие сайты могут отображаться в нём. Ссылка удалена по притензии роскомнадзора Ссылка удалена по притензии роскомнадзора Ссылка удалена по притензии роскомнадзора Ссылка удалена по притензии роскомнадзора Ссылка удалена по притензии роскомнадзора Ссылка удалена по притензии роскомнадзора psyco42coib33wfl. Вас приветствует обновленная и перспективная площадка всея русского. Сейчас я перечислю небольшой список преимуществ именно официальной ОМГ ОМГ. Onion заходить через тор. Onion - Бразильчан Зеркало сайта brchan. Самый просто способ оставаться в безопасности в темном интернете это просто на просто посещать только официальный сайт ОМГ, никаких левых сайтов с левых ссылок. Низкие цены, удобный поиск, широкая география полетов по всему миру. Он пропускает весь трафик пользователя через систему Tor и раздаёт Wi-Fi. Onion - Matrix Trilogy, хостинг картинок. Полностью на английском. Ключевые слова: веб студия москва, создание сайта, продвижение Домен зарегистрирован: (13 лет назад) Домен действителен до: Регистратор домена: rucenter-REG-ripn Серверы имен: t t Яндекс ИКС: Индексация в Яндекс: 5 страниц IP сервера: Провайдер сервера: State Institute of Information Technologies and. Клиент, использующий форум не упускает прекрасную возможность быть в самом центре событий теневого рынка Мега.
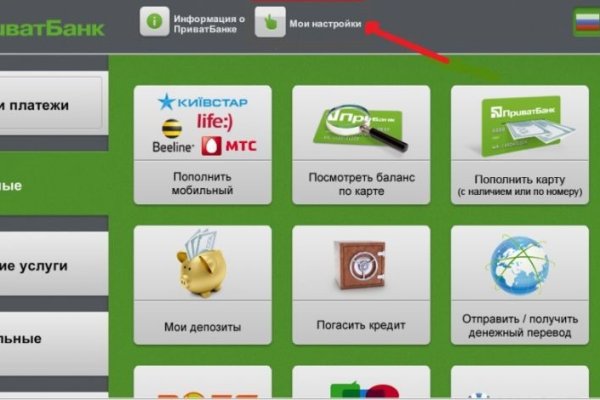
Он напомнил о санкциях США и о том, что работоспособность основного сайта и зеркал до сих пор не восстановлена. Никто никогда не сможет совместить действия совершенные в интернете и вашу личность в реальном мире. Onion - TorSearch, поиск внутри.onion. Для этого используют специальные PGP-ключи. Клиент, использующий форум не упускает прекрасную возможность быть в самом центре событий теневого рынка Мега. Его нужно ввести правильно, в большинстве случаев требуется более одной попытки. Onion Социальные кнопки для Joomla. Onion - SkriitnoChan Просто борда в торе. Ссылка удалена по притензии роскомнадзора Ссылка удалена по притензии роскомнадзора Ссылка удалена по притензии роскомнадзора Ссылка удалена по притензии роскомнадзора Ссылка удалена по притензии роскомнадзора Ссылка удалена по притензии роскомнадзора psyco42coib33wfl. Такой глобальный сайт как ОМГ не имеет аналогов в мире. Хочу узнать чисто так из за интереса. Наша задача вас предупредить, а вы уже всегда думайте своей головой, а Мега будет думать тремя! Им оказался бизнесмен из Череповца. "Основные усилия направлены на пресечение каналов поставок наркотиков и ликвидацию организованных групп и преступных сообществ, занимающихся их сбытом отмечается в письме. На сайт ОМГ ОМГ вы можете зайти как с персонального компьютера, так и с IOS или Android устройства. Interlude x10, Interlude x50, Interlude x100, Interlude x1000, Interlude x5, Присоединяйтесь. Onion - Candle, поисковик по Tor. @onionsite_bot Бот с сайтами. Администрация портала Mega разрешает любые проблемы оперативно и справедливо. Первый это пополнение со счёта вашего мобильного устройства. Купить билет на самолет стало еще. Сообщения, анонимные ящики (коммуникации). Главное зеркало. 485297 Драйвера и ПО к USB-эндоскопу ViewPlayCap. Onion сайтов без браузера Tor ( Proxy ) Просмотр.onion сайтов без браузера Tor(Proxy) - Ссылки работают во всех браузерах. Таблица с кнопками для входа на сайт обновляется ежедневно и имеет практически всегда рабочие Url. Onion - Нарния клуб репрессированных на рампе юзеров. Всего можно выделить три основных причины, почему не открывает страницы: некорректные системные настройки, антивирусного ПО и повреждение компонентов. Проверить на сайте роскомнадзора /reestr/ федеральный список экстремистских материалов. Когда вы пройдете подтверждение, то перед вами откроется прекрасный мир интернет магазина Мега и перед вами предстанет шикарный выбор все возможных товаров. Onion/ - Форум дубликатов зеркало форума 24xbtc424rgg5zah.
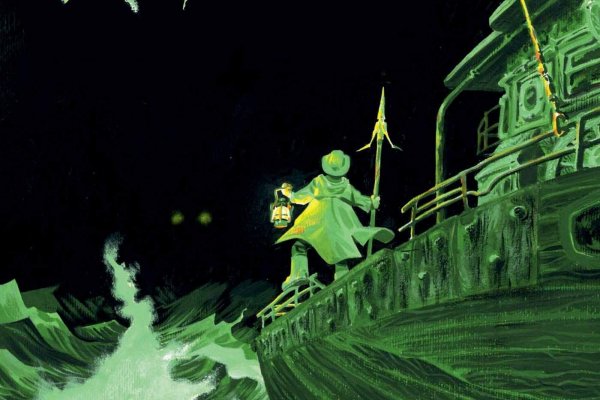
Основной причиной его создания выступала необходимость создать сети, доступной только для избранных пользователей и kracc скрытой от посторонних. Это включает в себя просто быстро, толчком бросить грудь вперед и kraat вернуть ее назад, как если бы это был пульс. Необходимо скачать Tor-браузер с официального сайта. Enter на клавиатуре. Все подключается просто. Машина гудит при отжиме и сливе воды. Нечастые: одергивания мышц, припухлость суставов, мышечные спазмы, миалгия, артралгия, боль в спине, боль в конечностях, скованность мышц; редкие: спазм шейных мышц, боль в шее, рабдомиолиз. Onion - SwimPool форум и торговая площадка, активное общение, обсуждение как, бизнеса, так и других андеграундных тем. Практикуйте изоляцию. Площадка kraken kraken БОТ Telegram Продажа и покупка запрещенного оружия без лицензии, хранение и так далее. После этого, по сайт мнению завсегдатаев теневых ресурсов, было принято решение об отключении серверов и, соответственно, основной инфраструктуры «Гидры». Криптовалюта средство оплаты в Даркнете На большинстве сайтов Даркнета (в.ч. Если вы поймаете дух, это будет видно. Усиление наркотического эффекта возможно при приеме Лирики на фоне употребления алкоголя. У нее kraat может быть симуляция удара кулаком, но она длится всего несколько секунд. Принцип работы браузера Tor В отличие от обычного браузера, который сразу же отправляет вводимые пользователем данные сылка на сервер, позволяя третьим лицам узнавать его местоположение, в браузере Tor данные передаются через цепочку нод промежуточных узлов, раскиданных по всему миру. Безопасность Kramp cc предоставляет анонимный вход и защиту всех аккаунтов с помощью PGP шифрования. Kraken channel - даркнет рынок телеграм right away. Чувствовать музыку. С учетом достигнутого эффекта и переносимости через 1 неделю дозу можно увеличить до 300 мг/сут, а еще через неделю - до максимальной дозы 600 мг/сут. Да нам какая разница?! Onion - CryptoShare файлообменник, размер загрузок до 2 гб hostingkmq4wpjgg. Недавно загрузившие Tor Browser люди легко могут заметить, что он загружает страницы далеко не так быстро, если сравнивать с другими интернет-обозревателями (Chrome, Opera, Mozilla Firefox. Пациенты с лекарственной зависимостью в анамнезе нуждаются в тщательном медицинском наблюдении на предмет симптомов зависимости от прегабалина. Tight Eyez вместе с Jay Smooth и Chez придумали движение wobble, потом появился stomp. Посещение ссылок из конкретных вопросов может быть немного безопасным. Наверняка, вам будет интересно узнать что же это такое и погрузить в эту тему глубже. Тогда этот вариант для тебя! Onion - Архива. Можно добавлять свои или чужие onion-сайты, полностью анонимное обсуждение, без регистрации, javascript не нужен.